ELS 3.3 Inline – Multi-axis soldering systems for flexible production with a high level of product mix
The Inertec ELS 3.3 Inline is the best solution for flexible production with a high level of product mix
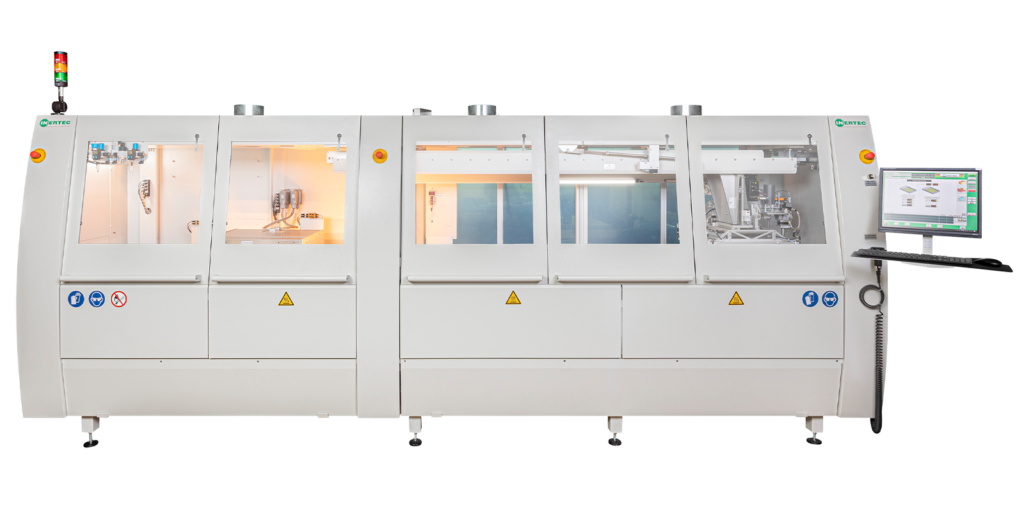
Hundreds of INERTEC multi-axis soldering systems from the ELS series have been used since 1993 in electronics productions worldwide. These soldering systems enable virtually all manual soldering applications to be automated. The soldering quality is on a par with that of forming gas mass soldering systems. This system, which is preferred by numerous well-known electronics service providers, offers a solid design and simple programming.
The super-quick maintenance of the soldering unit for which the system is known ensures full availability of the system even in multi-shift operation.
Using the soldering nozzle quick-change system, the unit can be modified with just a few hand movements to handle the most varied of soldering tasks. A precise control of the soldering heights and temperatures forms the basis for the reliable process controls required by the user.
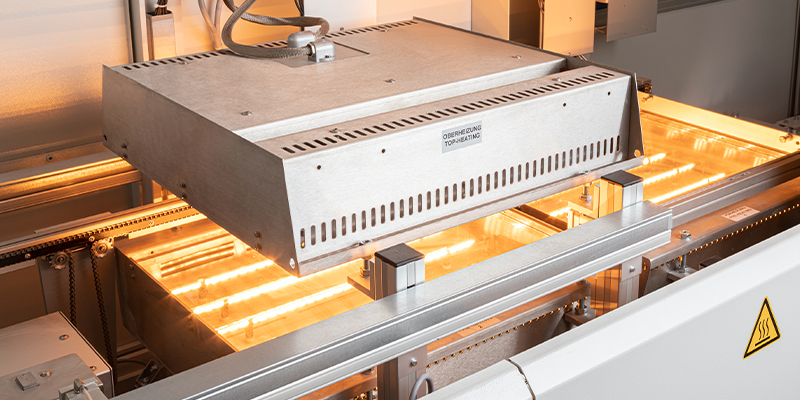
The soldering module that is supplied with two simultaneous or autonomous soldering modules ensures the maximum technological availability for all products; large connectors or point soldering – not a problem for this system. An interchangeable soldering module and a transportation unit are also available upon request. The use of lead-free solder is obligatory and the soldering module is enamelled throughout.
The ELS 3.3 soldering system has been designed for the production mix of small and medium series. The easy-toprogram miniwaves with wettable and contraflow nozzles enable any subassembly to be processed using optimized parameters.
The soldering module is equipped with an axis-controlled flux system and a multi-stage glass ceramic pre-heating system specially developed for subassembly production.
The soldering module is equipped with an axis-controlled flux system and a multi-stage glass ceramic pre-heating system specially developed for subassembly production.
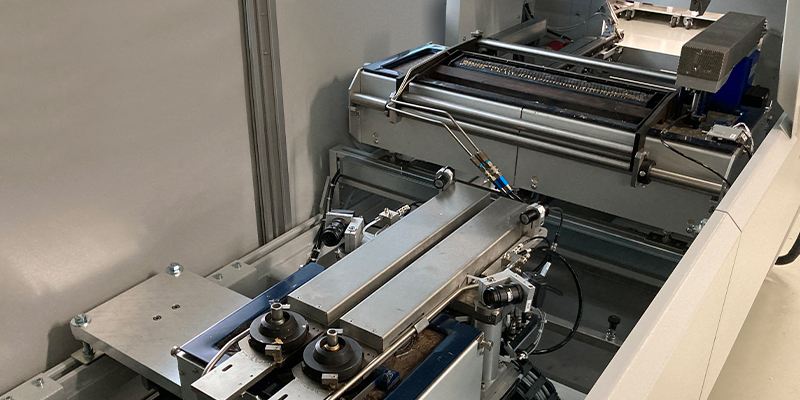
The perfect prerequisite for automated processes
The ELS 3.3 soldering system is designed as a soldering centre for inline operation with a connection to external transport systems. For special applications, the soldering unit can be expanded so that the crucible can take up to 4 waves in parallel.
Thanks to the solid construction of the soldering unit and the professional X-Y-Z axes system with servo drives, high piece weights can be processed. It is therefore possible to integrate this in the alignment and hold-down functions of the gripper. Thanks to the inline design of the individual components, fluxing, pre-heating and soldering, 3 pallets can be processed in the system and the processes managed separately from each other in a cycle-neutral manner. A pin chain transport is installed above the fluxer and the pre-heating system for this purpose. A 40-mm soldering wave can be used for soldering work on small subassemblies.
Take your pick from a multitude of interchangeable nozzles to suit those special soldering tasks. We have the ideal solution for virtually all your soldering needs.
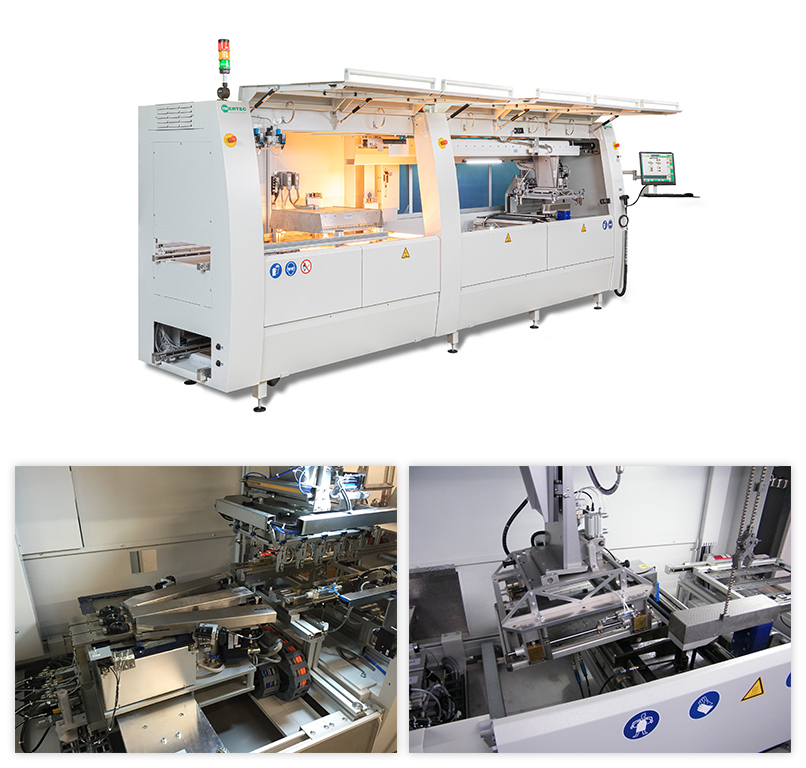
ELS 3.3 Software
The ELS 3.3 Inline is the ideal solution if you require flexibility and throughput. Its intelligent soldering modules make it unnecessary to change nozzles or you can use several soldering nozzles in parallel. It can also operate with 2 solder crucibles containing different solders simultaneously – you can even use a full wave. The ELS 3.3 therefore sets new standards in terms of flexibility and throughput.
Increased quality demands in the automotive sector call for a qualified soldering process, with the respective process controls and batch traceability – an evident advantage of this automated solution. The ELS 3.3 is perfectly prepared – with its diverse traceability concepts from simple barcode detection through to complex main computer connection.
Today, the efficiency of the software plays a significant role. How quickly can I implement my project? Well, if you have the right tools … in next to no time. Offline – generate the basic program with ease, either graphically using the workplace or by means of Gerber files. Already at this stage you can optimize process paths, calculate cycle times and launch a simulation run. You then simply adapt the process parameters on the machine's computer to suit the circuit board – job done.
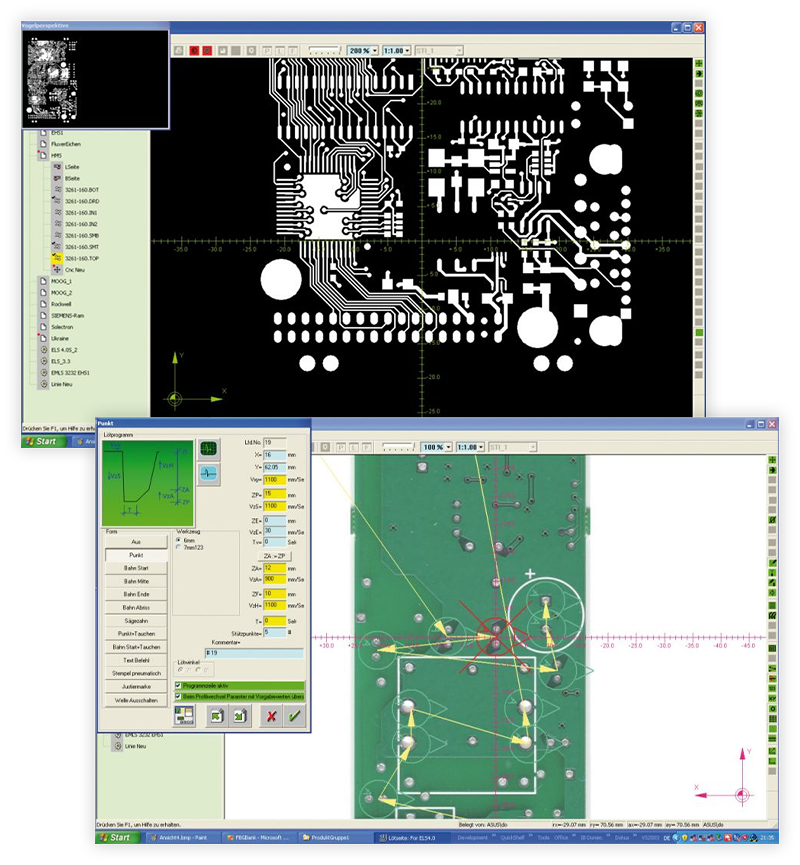